Why Formwork LVL is the Preferred Choice for Construction Professionals
In the ever-evolving world of construction, materials play a pivotal role in determining the success and efficiency of projects. Among the various options available, Formwork LVL (Laminated Veneer Lumber) has emerged as a popular choice among construction professionals. This article delves into the fundamental characteristics, roles, comparisons, environmental impact, and economic benefits of Formwork LVL, showcasing why it is favoured within the industry.
Understanding the basics of Formwork LVL
What is Formwork LVL?
Formwork LVL is an engineered wood product made from thin layers of veneer that are glued together. This process creates a composite material that is both strong and stable. It is particularly designed for use in formwork applications, where temporary structures are needed to shape and support fresh concrete until it hardens.
One of the key features of Formwork LVL is its consistent performance. Unlike traditional wooden beams, which may warp or twist over time, Formwork LVL maintains its shape and strength, ensuring that construction projects run smoothly and efficiently. This reliability is crucial, as any deformation during the curing process can lead to significant structural issues, necessitating costly repairs or even complete rebuilding.
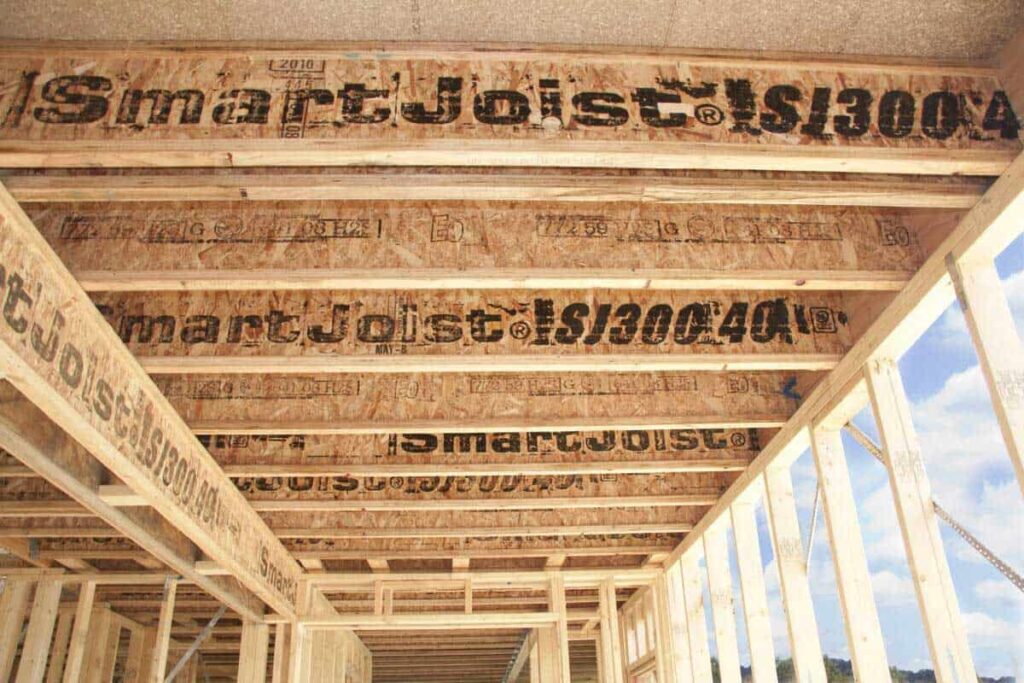
The unique properties of Formwork LVL
The manufacturing process of Formwork LVL lends it several unique properties. For starters, its high strength-to-weight ratio makes it incredibly versatile. Not only does it require less material than traditional methods, but it also offers superior load-bearing capabilities. This efficiency translates to reduced transportation costs and easier handling on-site, which can significantly expedite the construction timeline.
Moreover, Formwork LVL is resistant to moisture and environmental changes, further enhancing its durability. This makes it an excellent choice for construction sites that experience varying weather conditions. Its ability to withstand the rigours of both wet and dry environments means that contractors can rely on it to perform consistently, even in challenging climates. Additionally, the engineered nature of Formwork LVL allows for precise dimensions and uniformity, which is essential for achieving the desired finish in concrete structures. This precision reduces the need for extensive adjustments during installation, thereby saving time and labour costs.
Read about concrete plywood at: Concrete Plywood Durable Solutions for High-Performance Formwork
The role of Formwork LVL in construction
How Formwork LVL contributes to structural integrity
Structural integrity is paramount in construction, and Formwork LVL plays a crucial role in achieving this. Its engineered nature allows it to distribute loads evenly, reducing the risk of failure under pressure. This characteristic is particularly important when constructing high-rise buildings or large infrastructure projects. Find more about pressure on https://www.princeton.edu/~asmits/Bicycle_web/pressure.html
Furthermore, the dimensional stability of Formwork LVL helps to prevent issues such as deflection, sagging, or even collapse, leading to safer and more reliable structures.
The versatility of Formwork LVL in construction projects
Formwork LVL’s versatility extends to its adaptability in various construction scenarios. Whether it’s being used for walls, slabs, or foundations, it can be customised to meet the specific needs of each project. This flexibility enables construction teams to achieve their design goals more efficiently.
Additionally, its lightweight nature simplifies handling and installation processes, saving valuable time on the job site and reducing labour costs.
Comparing Formwork LVL with other construction materials
Formwork LVL versus traditional timber
When comparing Formwork LVL to traditional timber, significant differences become apparent. Traditional timber, while readily available, can be prone to warping and insect damage. In contrast, Formwork LVL is engineered for enhanced performance and longevity.
The uniformity of Formwork LVL also means that it can be produced in larger sizes and varying widths, making it more efficient for modern construction methods. Furthermore, it requires less maintenance over time, thereby making it a more reliable investment.
The advantages of Formwork LVL over steel and concrete
While steel and concrete are often lauded for their strength, they come with their own set of challenges, such as heavy weight and higher costs. Formwork LVL, on the other hand, presents a more balanced option. It is significantly lighter than steel and concrete while still delivering impressive load capabilities.
The ease of transport and installation that Formwork LVL provides can lead to increased productivity on site, translating to savings in both time and money. Moreover, the reduced carbon footprint associated with using engineered wood products positions Formwork LVL as a more sustainable option within the construction industry. Click here to learn more about carbon.
The environmental impact of using Formwork LVL
Sustainability aspects of Formwork LVL
Sustainability is a hot topic in construction today, and Formwork LVL aligns itself with eco-friendly principles. Being sourced from sustainably managed forests, the production of Formwork LVL minimises environmental impacts compared to traditional timber harvesting practices.
Additionally, the efficiency of wood as a building material helps in sequestering carbon in structures, contributing positively to the environment. This makes the choice to use Formwork LVL not just a practical decision but also a responsible one.

How Formwork LVL contributes to green construction
Green construction practices are all about reducing waste and energy consumption, and Formwork LVL fits perfectly into this model. Its lightweight nature reduces transportation emissions, and its efficient manufacturing process leads to less waste compared to that generated during traditional timber processing.
By opting for Formwork LVL, construction professionals can promote environmentally friendly practices while also achieving high-quality results.
The economic benefits of choosing Formwork LVL
Cost-effectiveness of Formwork LVL
Cost-effectiveness is a major concern in the construction industry, and Formwork LVL stands out in this regard. Although the initial costs may be higher than those of traditional timber, the long-term savings greatly outweigh these initial expenses.
Utilising Formwork LVL can lead to decreased material waste and reduced labour costs due to its easy handling and installation. This combination of factors makes it a financially sound choice for construction projects of all sizes.
The long-term financial advantages of using Formwork LVL
Over time, the durability and longevity of Formwork LVL contribute to significant economic benefits. Projects that utilise Formwork LVL are less likely to incur maintenance costs associated with repairs or replacements of inferior materials.
Moreover, the higher resale value of structures built with Formwork LVL can lead to increased profitability for developers, making it not just a smart material choice but ultimately a wise financial investment.
In conclusion, Formwork LVL has proven itself to be a preferred choice among construction professionals for a multitude of reasons. Its unique properties, structural integrity, cost-effectiveness, and environmental benefits collectively make it a frontrunner in modern construction practices. As the industry continues to evolve, adopting materials like Formwork LVL will likely pave the way for sustainable and efficient building solutions.